Industrial Vibration Monitoring: Key to Predictive Maintenance
Table of Contents
- Introduction to Industrial Vibration Monitoring
- Working Principle of Vibration Monitoring
- Technologies Behind Vibration Sensors
- Applications of Industrial Vibration Monitoring
- Benefits of Vibration Monitoring in Industry
- Challenges in Industrial Vibration Monitoring
- The Future of Industrial Vibration Monitoring
Introduction to Industrial Vibration Monitoring
Industrial vibration monitoring refers to the use of sensors to detect and measure vibrations in industrial equipment such as motors, pumps, compressors, and turbines. Monitoring vibrations helps to identify potential problems, enabling early detection of mechanical faults, and ensuring the smooth operation of equipment. By continuously monitoring vibration levels, industries can move from reactive to proactive maintenance strategies, which significantly reduces downtime and maintenance costs.
Working Principle of Vibration Monitoring
Vibration sensors work by detecting the motion or oscillation of an object. These sensors convert mechanical vibrations into electrical signals, which are then analyzed to detect irregularities. The most common types of vibration sensors are:
- Accelerometers: These sensors measure the acceleration or deceleration of an object, providing data on the amplitude and frequency of vibrations.
- Displacement Sensors: These sensors measure the displacement of a vibrating object, offering insights into the size and extent of vibration movement.
- Velocity Sensors: These sensors detect the velocity of an object in motion, giving important information on the rate of change in vibration.
Data from these sensors is analyzed using specialized software to detect abnormalities such as excessive vibration, which can indicate problems like misalignment, imbalance, or bearing failure in industrial machinery.
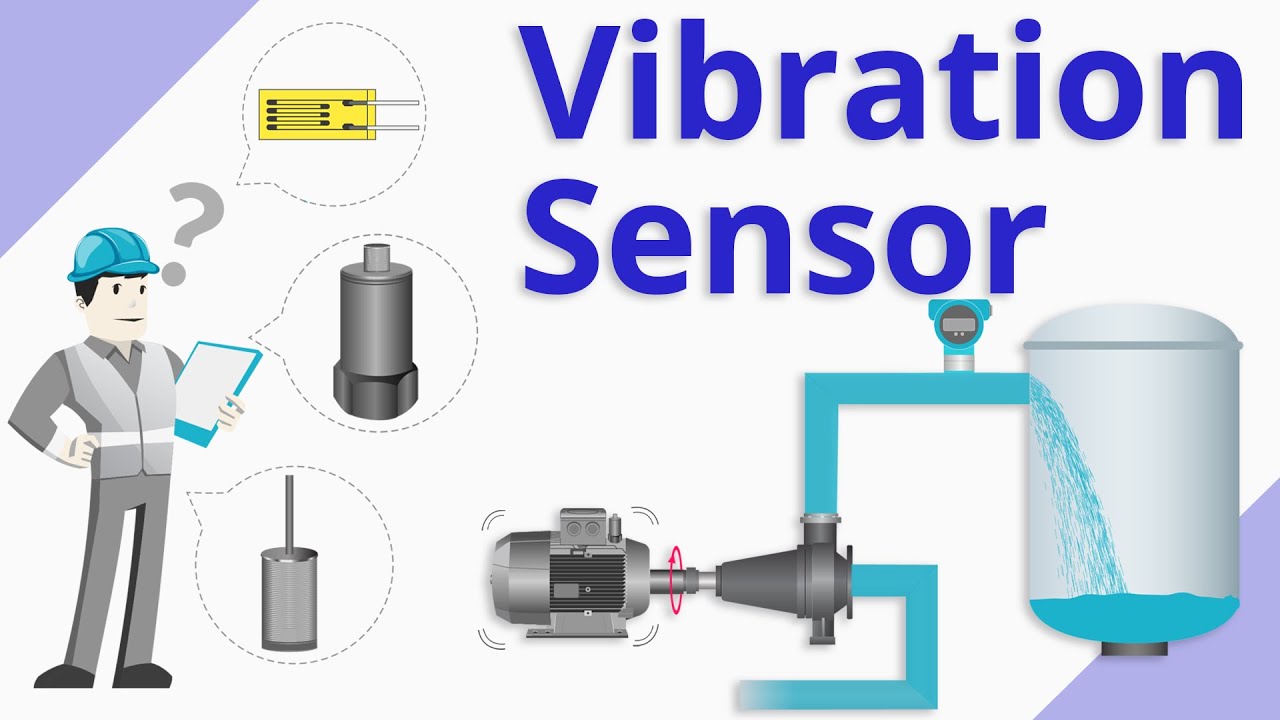
Technologies Behind Vibration Sensors
Industrial vibration monitoring systems rely on various technologies to ensure accurate and real-time monitoring of machine health:
- Piezoelectric Technology: This technology is commonly used in accelerometers. It generates electrical charge when subjected to mechanical stress, allowing it to measure vibrations with high sensitivity.
- Electromagnetic Sensors: Electromagnetic vibration sensors work by detecting changes in the position of a vibrating mass within a magnetic field, which generates an electrical signal.
- Strain Gauge Technology: Strain gauges are used to detect changes in an object’s shape due to stress, which is then translated into vibration measurements.
- Wireless Vibration Monitoring: IoT-enabled wireless vibration sensors allow for remote monitoring of equipment, providing real-time data without the need for wired connections.
Applications of Industrial Vibration Monitoring
Vibration monitoring is essential for various industrial applications, including:
- Predictive Maintenance: Monitoring vibrations in machinery helps predict failures before they occur, enabling timely repairs and reducing unexpected downtime.
- Condition Monitoring: Continuous vibration monitoring helps assess the condition of equipment and identifies performance degradation, helping to maintain optimal operation.
- Quality Control: Vibration sensors are used to ensure the consistency and quality of manufactured products, especially in industries like automotive and aerospace.
- Safety: Detecting abnormal vibrations in critical machinery such as turbines, motors, or pumps can help prevent catastrophic failures and enhance workplace safety.
- Process Optimization: Vibration data can be used to fine-tune machinery settings, improving efficiency and energy consumption in industrial processes.
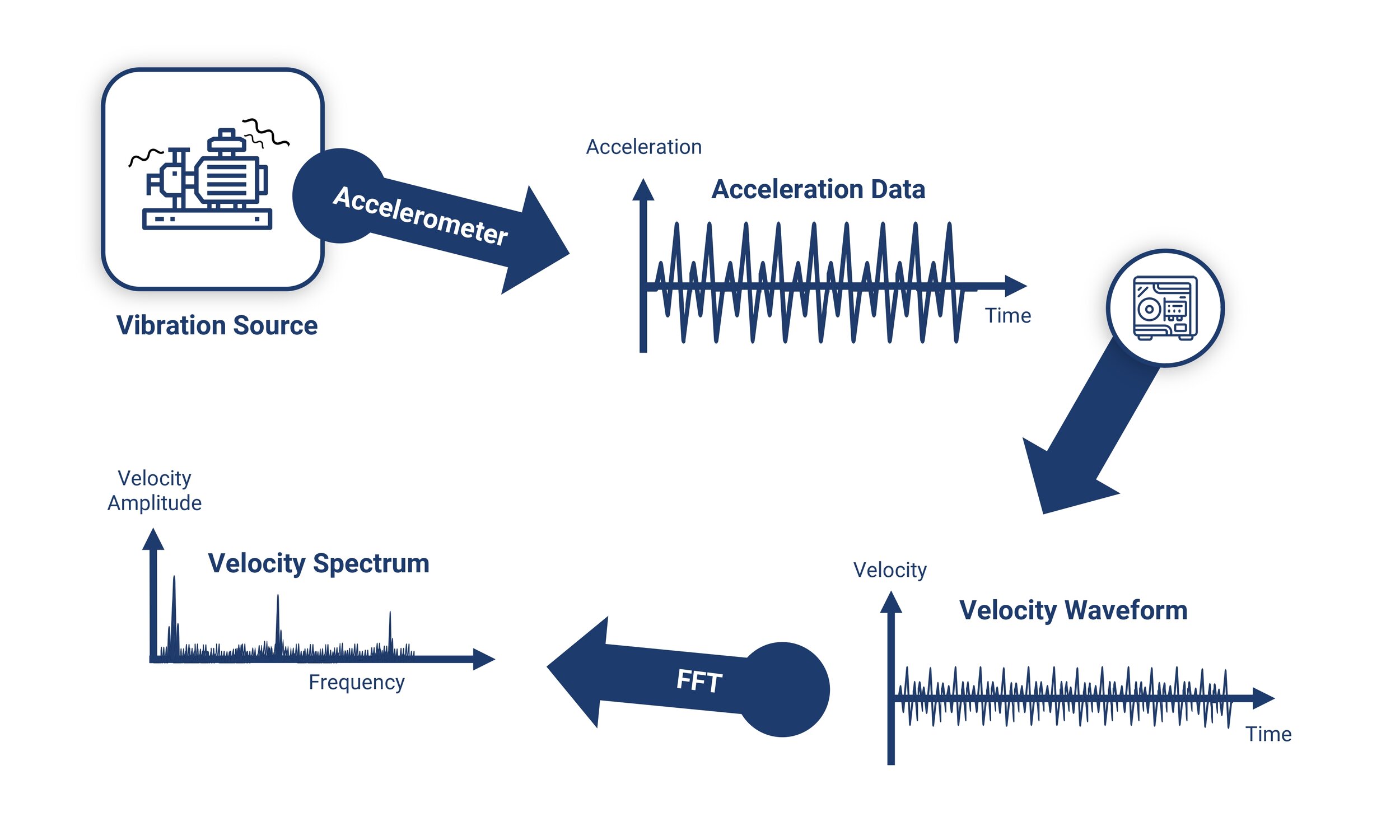
Benefits of Vibration Monitoring in Industry
Industrial vibration monitoring systems provide numerous benefits for businesses, including:
- Reduced Downtime: By identifying issues early, vibration monitoring helps avoid costly downtime, keeping production lines running smoothly.
- Lower Maintenance Costs: Predictive maintenance reduces the need for emergency repairs and unnecessary part replacements, leading to significant cost savings.
- Improved Equipment Lifespan: Regular monitoring ensures that machines are maintained before issues become severe, extending the life of critical assets.
- Enhanced Safety: Vibration monitoring helps detect faults in time, reducing the risk of equipment failure that could lead to safety hazards.
- Data-Driven Decision Making: Vibration data helps engineers and operators make informed decisions about when to service equipment and when to implement upgrades.
Challenges in Industrial Vibration Monitoring
While vibration monitoring offers significant benefits, there are also challenges associated with its implementation:
- Data Overload: The large volume of vibration data collected can overwhelm operators, making it challenging to identify meaningful patterns without proper data analysis tools.
- Installation Costs: Setting up a vibration monitoring system, especially one with wireless sensors and advanced analytics, can be expensive.
- Calibration Issues: Ensuring sensors are properly calibrated is crucial for accurate measurements, and improperly calibrated systems can lead to inaccurate readings.
- Environmental Factors: Vibration sensors can be affected by environmental factors such as temperature fluctuations, humidity, and external vibrations from nearby equipment.
The Future of Industrial Vibration Monitoring
The future of industrial vibration monitoring looks promising with ongoing advancements in sensor technology and data analytics:
- AI and Machine Learning Integration: The use of AI and machine learning algorithms will help to analyze large datasets, identify hidden patterns, and predict failures with greater accuracy.
- Edge Computing: Edge computing will allow for faster analysis of vibration data at the sensor level, reducing the need for constant cloud communication and improving real-time decision-making.
- Wireless and IoT Solutions: Wireless IoT-enabled vibration monitoring systems will become more widely adopted, enabling remote monitoring and reducing installation complexity.
- Increased Automation: Vibration monitoring systems will be increasingly integrated with automated control systems, enabling automatic adjustments to equipment based on real-time vibration data.
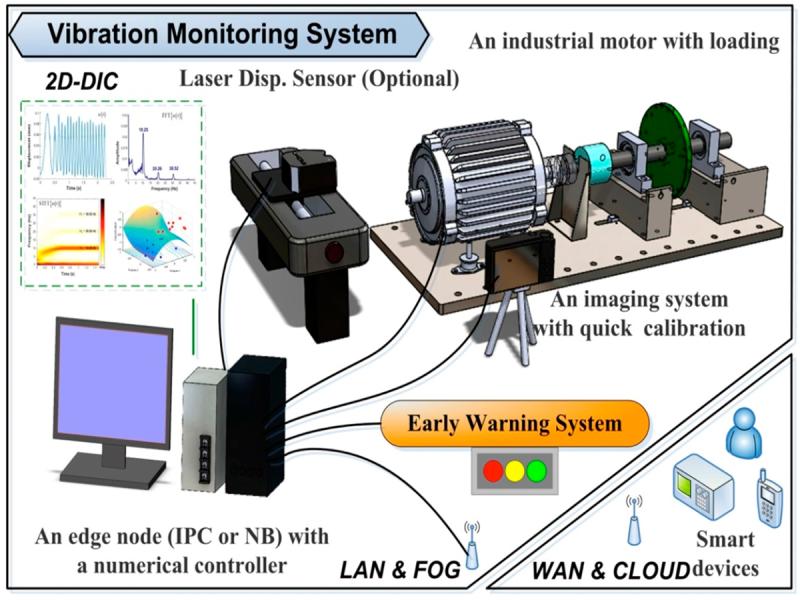